April 27th, 2020
After looking back on this past year’s schedule, we would like to make some remarks for next year’s team to improve. In the future we would recommend fundraising for the project’s expenses over the summer, prior to the semester starting in September. During the fall semester we were busy with initial design testing and our ASCE student chapter did not have time to help with our fundraising efforts. If fundraising efforts were started in June, both our team and ASCE could have spent more time and effort to bring support for the project.
In addition, we would recommend finalizing all design selections with a completed structural analysis by the end of the fall semester. It was hard to communicate with each other over winter break and make a final design selection. Because of this, the structural analysis was not completed until the first week of February which delayed the arrival of the foam mold. If the design was completed in December, the mold could have been designed and fabricated over winter break and would ideally be ready for construction at the start of the spring semester.
April 26th, 2020
During the fall semester the team was able to fundraise $2,850.00 from our generous sponsors. We would like to thank you all again for donating, as this project would not have been possible without your support. The necessary materials for construction and testing were purchased through the semester, and an expense report was generated to track the project’s budget. The final cost for materials and supplies came out to $2,053.76 for the project’s completion up to this point. Unfortunately, the canoe was left unfinished due to the national health crisis and items such as the spray foam and waterproofing were not able to be purchased. Overall, it is important to note the project is currently under budget and about 90% completed. The remaining supplies that will be needed in the future can be purchased within the budget remaining to obtain final testing results.
The project has been through minor delays over the course of its duration however at this point in time we are up to date with the major milestones remaining. The competition has been canceled and the team is currently working on finalizing reports and presentations for TCNJ. Until it is safe to gather on campus the canoe will remain unfinished. A tentative schedule of when the team will work on finishes and final testing of the canoe will be decided at a future date.
March 25th, 2020
The team has stopped progress on building the canoe. Just last week, all Student Conference activities and the ASCE 2020 National Concrete Canoe Competition were canceled by the ASCE President and Executive Director because of the recent COVID-19 pandemic. In addition, TCNJ closed all academic buildings including Armstrong Hall, where the canoe was being constructed. This forced the team to make a decision to stop working on the canoe. Even though we were nearly done with finishing the prototype, the team understands that our health and the safety of the public is more important than finishing the canoe at this time. This is disappointing for all of us. We hope to return to finishing the canoe and test the prototype on water once we are safe to do so.
The canoe was monitored every two days after the pour to make sure the concrete was moist and curing properly. It is crucial to monitor the concrete cure on a frequent basis to ensure the canoe will not crack. A burlap cloth was kept moist on the curing concrete while a clear tarp covered the table to ensure the moisture stayed on the burlap. A few images of the canoe during curing can be seen below:
The team was able to monitor the cure until the 10 day strength. The next step was to remove the mold and set the canoe in stands. Due to the public health issue, the canoe was not taken from the mold and is now stored away until the team can work on it again. We will now be focusing on our reports and presentations for TCNJ.
March 18th, 2020
After finalizing our design, the team set up and practiced our method of construction in the newly renovated Armstrong Hall laboratory. The team tested the mortar sprayer and worked on application techniques prior to the pour date. It was decided to use a combination of hand placement and the mortar sprayer to apply the first ¼” layer of concrete onto the canoe mold. The fiberglass mesh was prepared and cut into various lengths so that it can easily be applied to the concrete in a fast and effective manner. The most important factor during the pour will be how fast the concrete will dry. This required the team to work quickly and effectively during the entire pouring process. The final layer of concrete was applied with the mortar sprayer and hand troweled to a smooth finish.
With the help from the aspiring Junior class concrete canoe team, we were able to pour the canoe in 3 hours! This proved that our mortar spraying technique not only reduced pour time, but it also made it easier to apply the concrete on the mold. Please refer to the following images that show the construction progress:
The canoe is currently curing in the Armstrong parking garage due to the current access restrictions on academic buildings on TCNJ’s campus. We have been monitoring the canoe every two days, making sure that the burlap cloth is moist to avoid cracking the concrete during its curing process. The team plans to remove the mold next week and transport the canoe to a different location off campus to finish sand and apply waterproofing.
February 28, 2020
In the middle of January, the mix design team finalized the mix for this year’s Concrete Canoe. The mix was made up of the following materials: Portland Cement Type IL, Poraver, Elemix, Perlite, and sand. The percentages by volume of the materials are shown in the table below. The remaining percentage is the volume of water for our mix.
Portland Cement | 16% |
Elemix | 36% |
Poraver | 22% |
Perlite | 5% |
Sand | 5% |
This mix has a 28 days strength of 350 PSI, which exceeded the amount of strength needed for our hull design. Additionally the unit weight of this mix is 45 PCF which, based on the volume of the canoe, would give us a canoe around 150 pounds. A 150 pound canoe is the optimal hull design based on the loading conditions calculated for buoyancy. The loading conditions were based on the sprint and slalom races. Foam will later be added to the bow and stern of the canoe to design for the swamp test loading conditions.
However, upon contacting companies for materials we discovered that Elemix was not able to be obtained due to the manufacturer going out of business in the Summer of 2019. Elemix made up 36% of our final mix design. Due to the inability to get Elemix, and the absence of any easy replacements, the mix design team has decided to replace the Elemix with a mix of perlite and sand. Elemix is a lightweight replacement for fine and coarse aggregate. Therefore, Perlite and sand are a natural substitute for Elemix. However, the team will do several quick 7 days test in order to determine the right percent of Perlite and sand to replace the Elemix that will still give a similar strength and unit weight of our original mix.
February 26, 2020
After the team enjoyed their time off for winter break, we came back for our final semester at TCNJ. Once the shape and dimensions of the canoe were finalized, a structural analysis was completed using Microsoft Excel. This was done to determine the compressive strength needed from the mix design. With cross section outputs from DELFTship, shear and moment diagrams were created for two loading scenarios, which are two paddlers and four paddlers in the canoe. The self-weight of the canoe, which is calculated to be about 150 pounds, and an assumed paddler weight of 180 pounds was taken into account during the development of these graphs. Along with this, a displacement of 3.9 feet between paddlers was used in the calculations. The diagrams of the more critical condition, which is with four paddlers in the canoe, can be seen below:
When the shear diagram was complete, shear equations were able to be produced based on trendlines. These equations were then integrated to find the moment equations. The moment equations were used to create the moment diagram and determine the maximum moment of the canoe, which is 250.9 lb-ft at 9.6 feet from the bow. With the maximum moment found, the hull design team could complete the compressive strength analysis. The calculations for this value resulted in a strength of 41.5 psi. The team decided to also add a factor of safety of 3 to this value, which results in a strength of 124.5 psi. The compressive strength found with this analysis was used by the mix team to determine an appropriate mix for the canoe.
November 30, 2019
The mix design team has begun receiving sample material that have been requested. A sample of Portland Cement Type IL was received in time for the teams second round of testing. From the first round of testing, the team was able to determine that the water:cement ratio of mix #3 is optimal because it was the only mix that would be able to be sprayed. However, mix #3 also had a high unit weight that is not ideal for the floatability of the canoe. Using that knowledge, the team created four different mix design, #4-#7 each with a different percentage of porver. Additionally, mix #5 had the same percentage of porver as mix #4, but used Portland Cement Type IL rather than the standard Portland Cement. The results of testing are shown in the table below.
Mix Number | Percentage of Porver | Water:Cement Ratio | Unit Weight (pcf) | Compressive Strength (psi) |
4 | 22% | 0.94 | 49.55 | 471.72 |
5 | 22% | 0.94 | 52.42 | 640.89 |
6 | 20% | 0.94 | 51.91 | 548.66 |
7 | 24% | 0.94 | 48.26 | 378.44 |
The test results came out largely as expected. However, the team was pleasantly surprised by the strength yielded by Portland Cement Type IL. The mix design team plans on creating another set of mixes to test in the coming days. The focus of this testing will be to look into the use of Portland Cement IL and the use of Perlite, which is a new aggregate to replace sand in our mixes.
November 15, 2019
The hull design team has begun preparation for laboratory testing. Utilizing on campus resources, Matt and Justyn worked with TCNJ’s Lab Technician, Brian Wittreich, to 3D print the three alternative hull designs. Due to the 3D printing design constraints, the models were scaled down to 1/25 size. The next step going forward will be working with advisor Dr. Michael Horst and Dr. Lisa Gregga to test the canoe prototypes in an open channel flow. The results we are looking for is a drag coefficient for each canoe. The results of each design will be compared to each other to provide technical support on our final design decision.
October 30, 2019
Hull Design:
The hull design team has narrowed it down to three alternative designs:
- Straight sides, low rocker, shallow v bottom
- Straight sides, low rocker, shallow arch bottom
- Straight sides, low rocker, round bottom
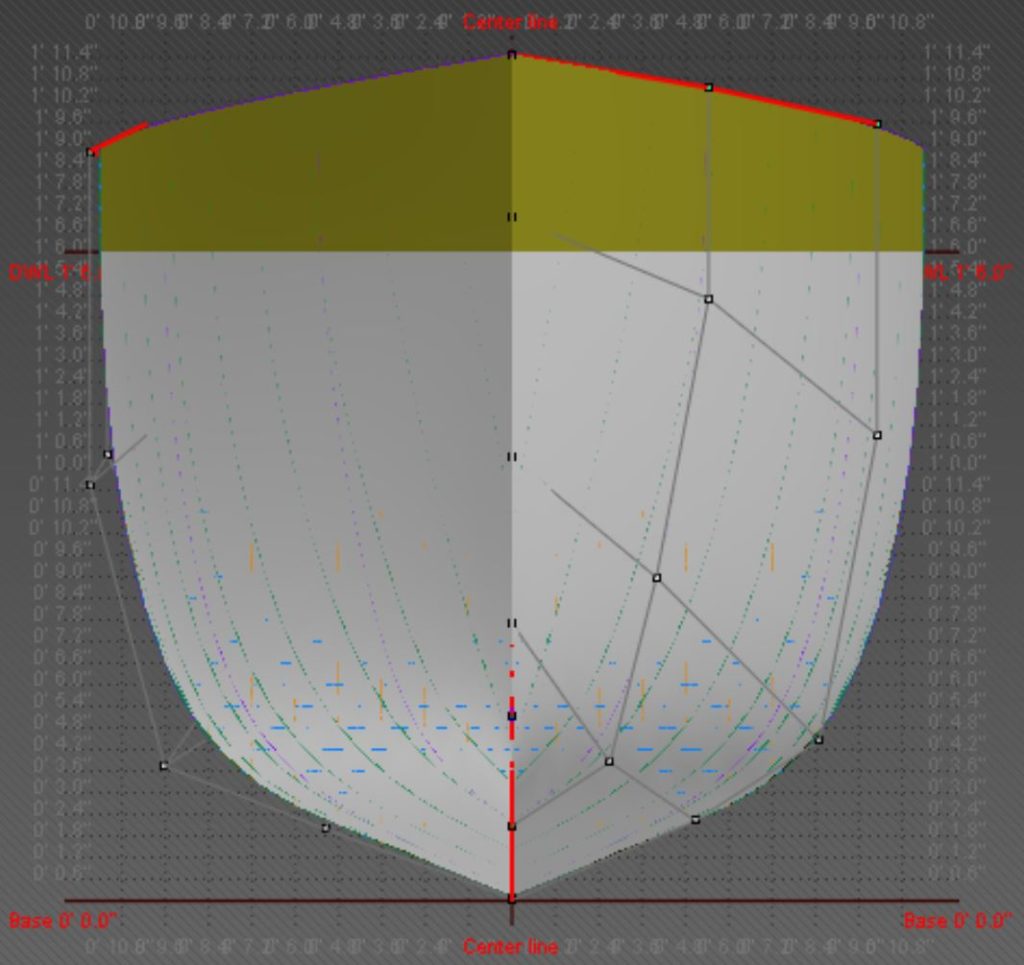


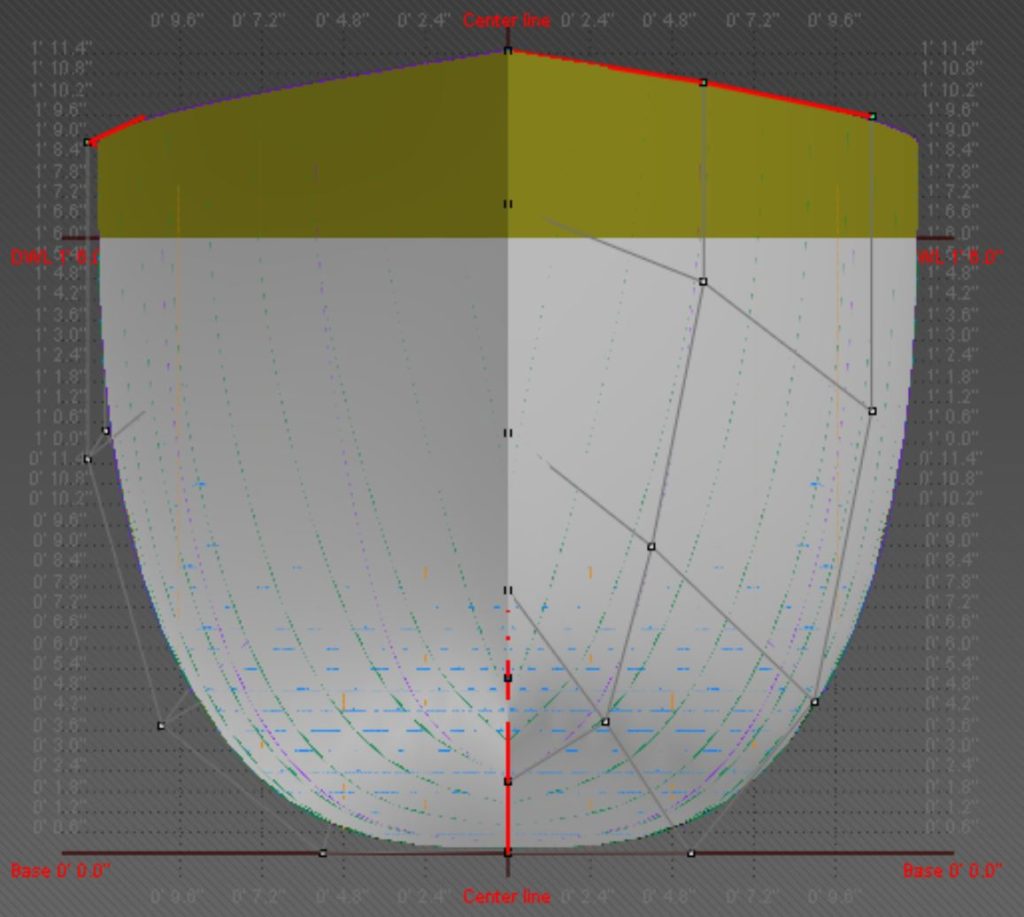


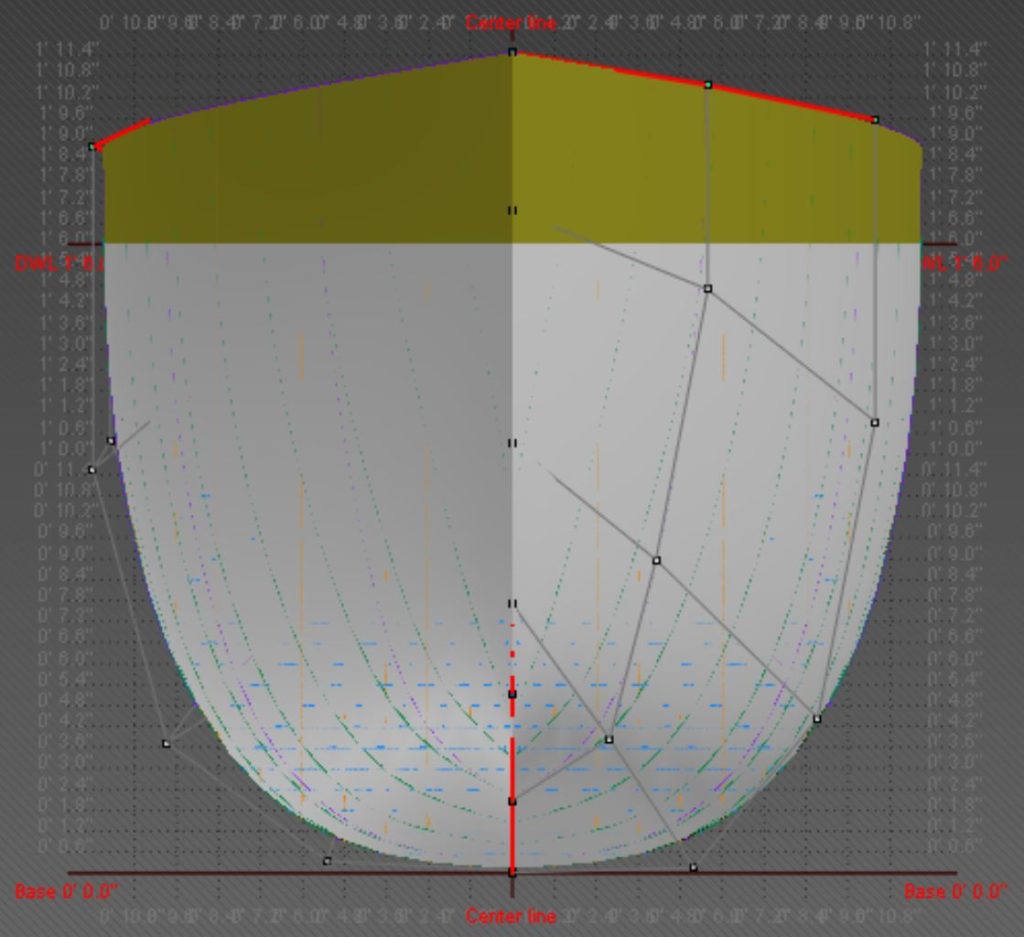


These designs were found using a decision matrix weighing the pros and cons of each hull profile in speed and stability. Furthermore, design and constructability were also taken into consideration. The optimal hull design is canoe 1 being a canoe with straight sides, low rocker, and a shallow v bottom.
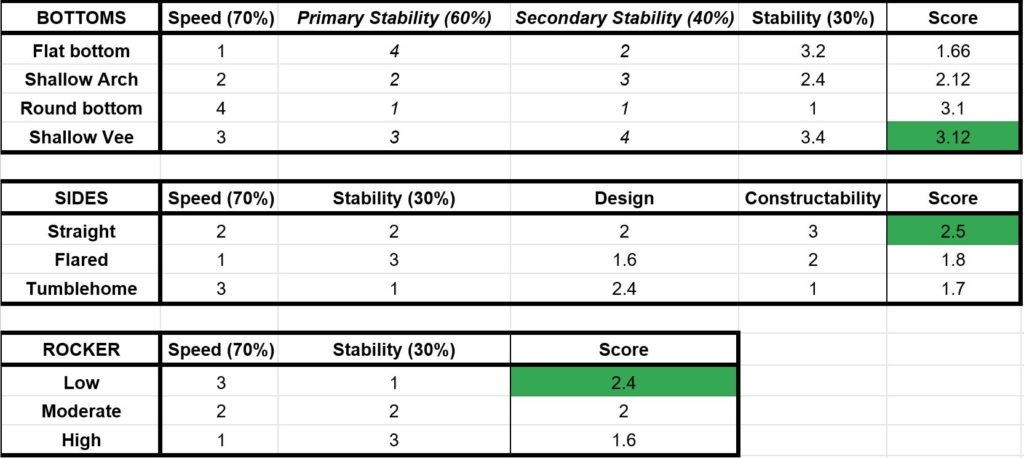
Once the alternative hull designs were found, an analysis was completed on possible lengths and widths for the three alternative designs. Optimization for these two aspects was carried out by comparing froude numbers and length-to-beam ratios. By researching this topic, the ideal froude number for a canoe is 0.4. The length and beam with calculated froude numbers closest to this value were chosen as optimal. Additionally, the higher the length-to-beam ratio, the more efficient the boat will be. The values for each of these aspects were used in our final hull design decision.
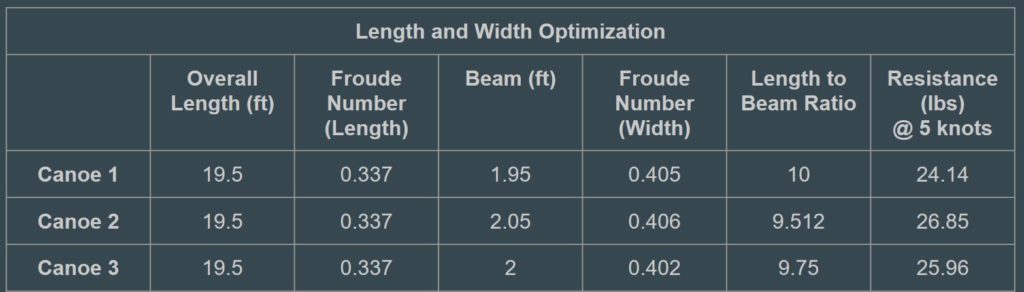
Mix Design:
The mix design team has closed on on four alternative designs:
- Standard mix with low water cement ratio and standard poraver
- Same as standard water cement ratio with less poraver
- High water cement ratio with less poraver
These mix designs were selected and analyzed using a decision matrix. The decision matrix took into account the floatability, strength, and workability. The third option with a high water cement ratio with less poraver was determined to be the optimal design from the decision matrix. This mix allows the team to use a mortar sprayer because of the better workability that comes from the higher water cement ratio. Additionally, less poraver is ideal for a mortar sprayer because the aggregates are less likely to clog the sprayer when the canoe is being created.
Mix Number | Water:Cement Ratio | Unit Weight | Compressive Strength |
1 | 0.77 | 49.20 pcf | 205 psi |
2 | 0.77 | 57.42 pcf | 377 psi |
3 | 0.95 | 60.38 pcf | 375 psi |
Based on the initial testing showing in the figure above, the floatability and strength of the mix will not be compromised by choosing the third alternative. The team will conduct further testing in the laboratory to determine the optimal percent of aggregates that will allow for a lightweight mix that will still have enough strength to withstand the four team members on competition day.
Mold Design:
The project team has closed on on four alternative designs:
- Male mold laser cut from foam
- Female mold laser cut from foam
- Male mold made from wood
- Male mold pressed into female mold
These mold designs were selected and analysed based on previous teams designs. Each option was put into a decision matrix, weighing cost, constructability, and the quality of finish. The Male mold laser cut from foam scored the highest out of all four options. This mold will have to be constructed by an outside company and assembled by the team once in shop. A male mold laser cut from foam is one of the more expensive options and will take up the largest amount of our budget. The team will have to rely on sponsors to donate funding to continue with this design. The mold will allow us to effectively use a mortar sprayer to apply the concrete and allow us to hand finish the outside surface of the canoe.
October 17, 2019
Our team has continued research on the design and identified the project constraints. The hull design team has created a design matrix to weight standard design options for various cross-sections, side profiles, and rockers. We are currently investigating software packages to model various design options and calculate resistance factors. The mix design team has come up with a list of materials they would like to test in lab. After testing the team will be able to come up with alternative design options for the concrete mixture.
Throughout this process the team is being conscious of constructability. Our research has provided clarity on what designs will work and which ones will not work with the given constraints. The team understands that our preparation work will make or break how successful the canoe will be during the competition.
September 29, 2019
The team has begun to brainstorm methods of constructing the canoe. The mix design team is currently reaching out to local companies to donate extra materials for mix testing. We have decided to practice building the canoe on an old female mold this semester. This will allow us to test our method of applying the concrete with a spray gun. In addition, Olivia has begun researching any safety items the team should be aware of during construction, transportation, and competition.
The hull design team has begun to brainstorm various shapes and sizes for the canoe. The length of the canoe will affect its top speed as well as its maneuverability. The team wants to focus on having a smooth outside finish on the canoe in order to have as minimal resistance as possible during travel. Constructing the canoe with a male mold will allow the team to finish the outside concrete by hand. Constructing the canoe with a female mold will allow the team to finish the concrete exposed on the outside of the canoe, making it more difficult to control the finish.
September 17, 2019
Our team is currently progressing in fundraising money for the project and forming a preliminary schedule. If you are interested in becoming a sponsor, please reach out to us!
The team has begun researching the results from the 2019 ASCE Concrete Canoe Competition. The mix design team is finding the aggregates used by the 2019 winning teams. The hull design team is finding the canoe sizing specifications used by the 2019 winning teams.
Lastly, the 2020 Rules and Regulations were recently released. The 2020 TCNJ team is reading up on the rules and familiarizing ourselves with the given design constraints.