David Crain – Computer Aided Design / Secretary
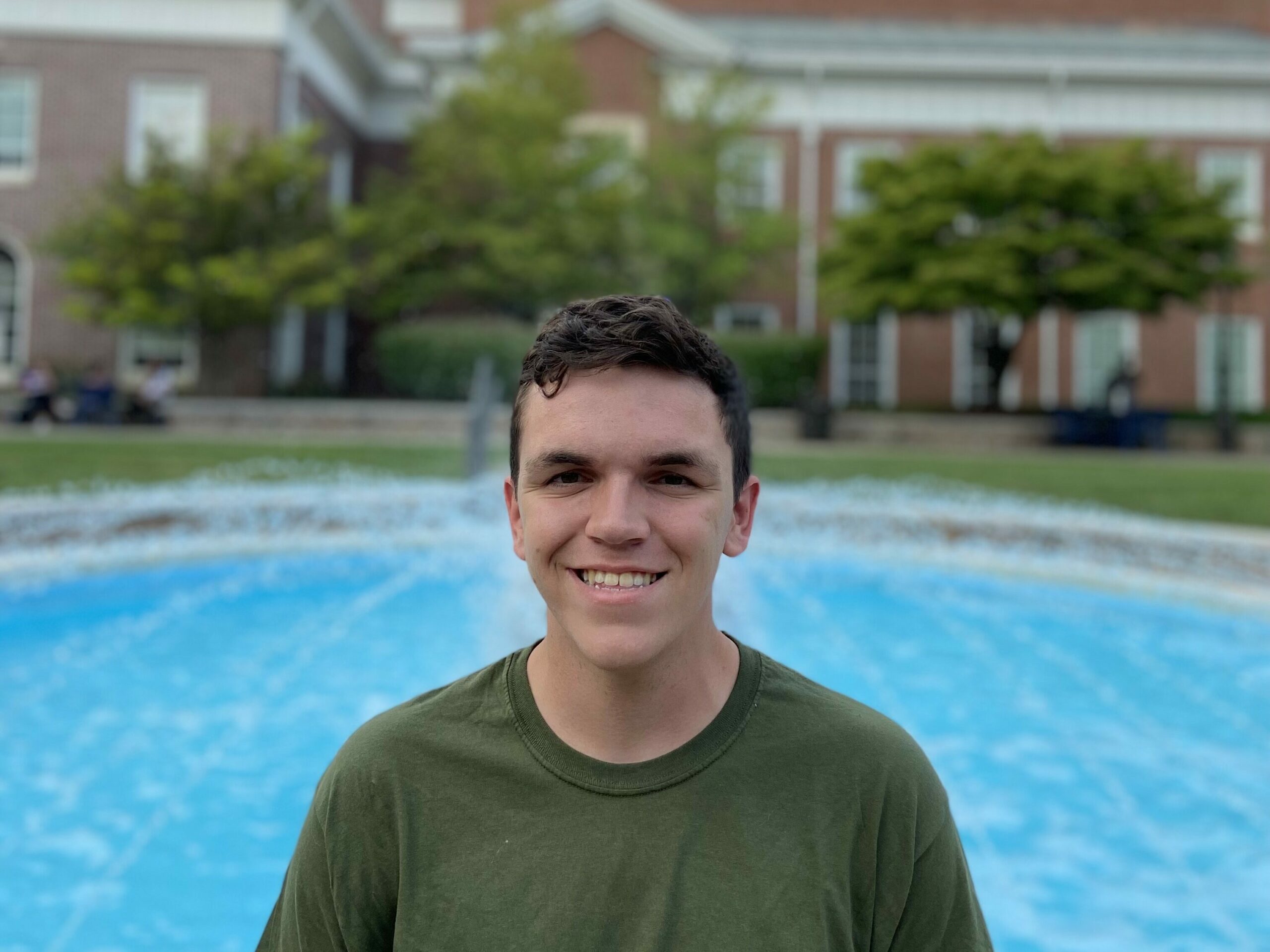
David Crain was responsible for the CAD modeling of the device and aided with the finite element analysis. Along with Eugene, he led the process of machining device parts and fabricating the device. David was also in charge of recording the meeting minutes, developing and maintaining the Gantt chart, as well as any other record keeping.
John Goldinak – Biomechanical Analyses / Budgetmaster
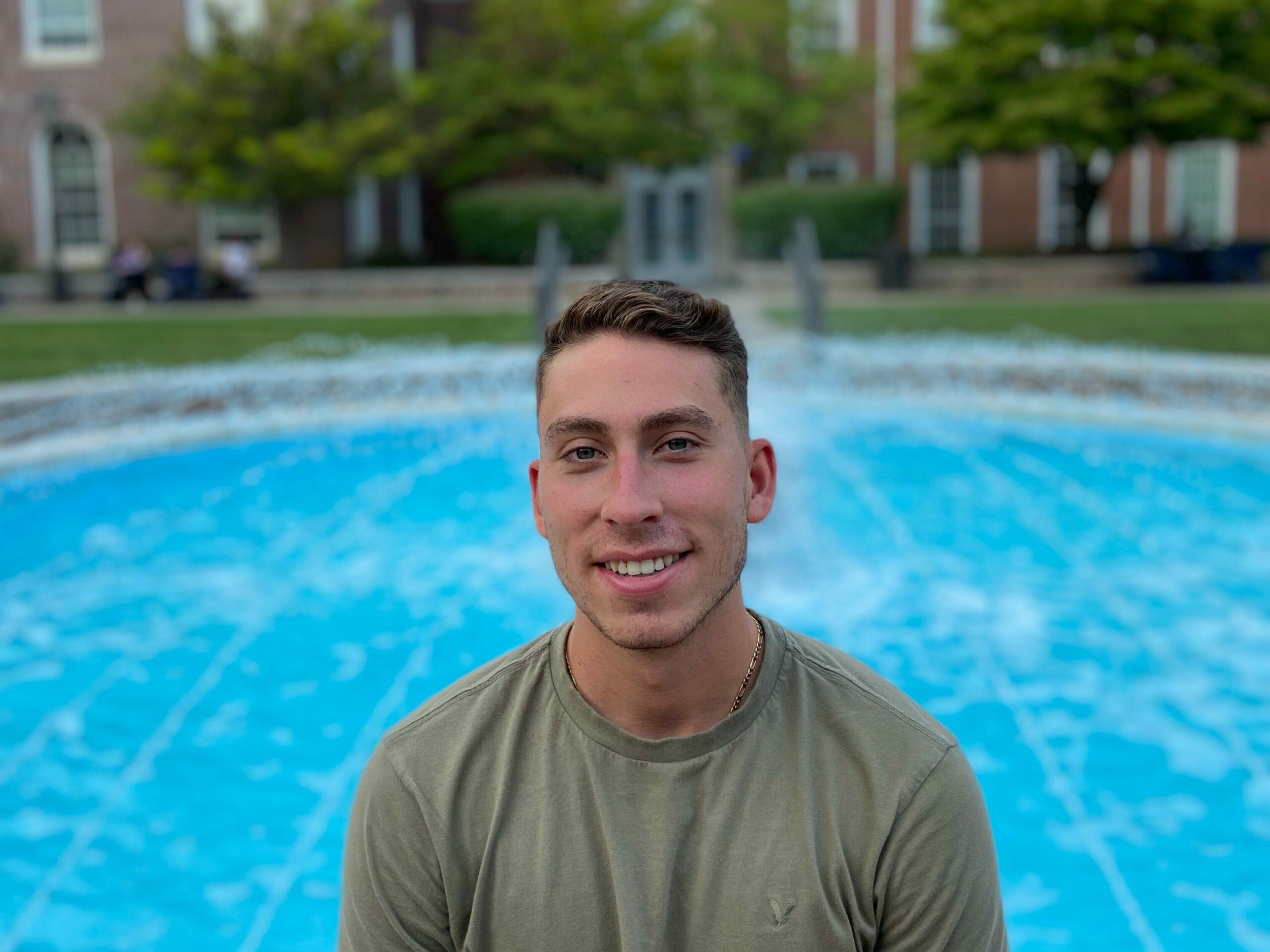
John Goldinak was responsible for implementing, verifying, and validating the electronic system with Spencer Haber. John also helped machine and fabricate the reinforced spring-like curve as well as the device frame, and performed both verification and validation tests on the mechanical aspects and electrical aspects of the device. He, along with Spencer, performed the spring constant and energy expenditure estimations. Furthermore, John was in charge of keeping track of the costs throughout this project and ordering both the device components and device materials.
Spencer Haber – Electronic Systems & Programming / Team Leader
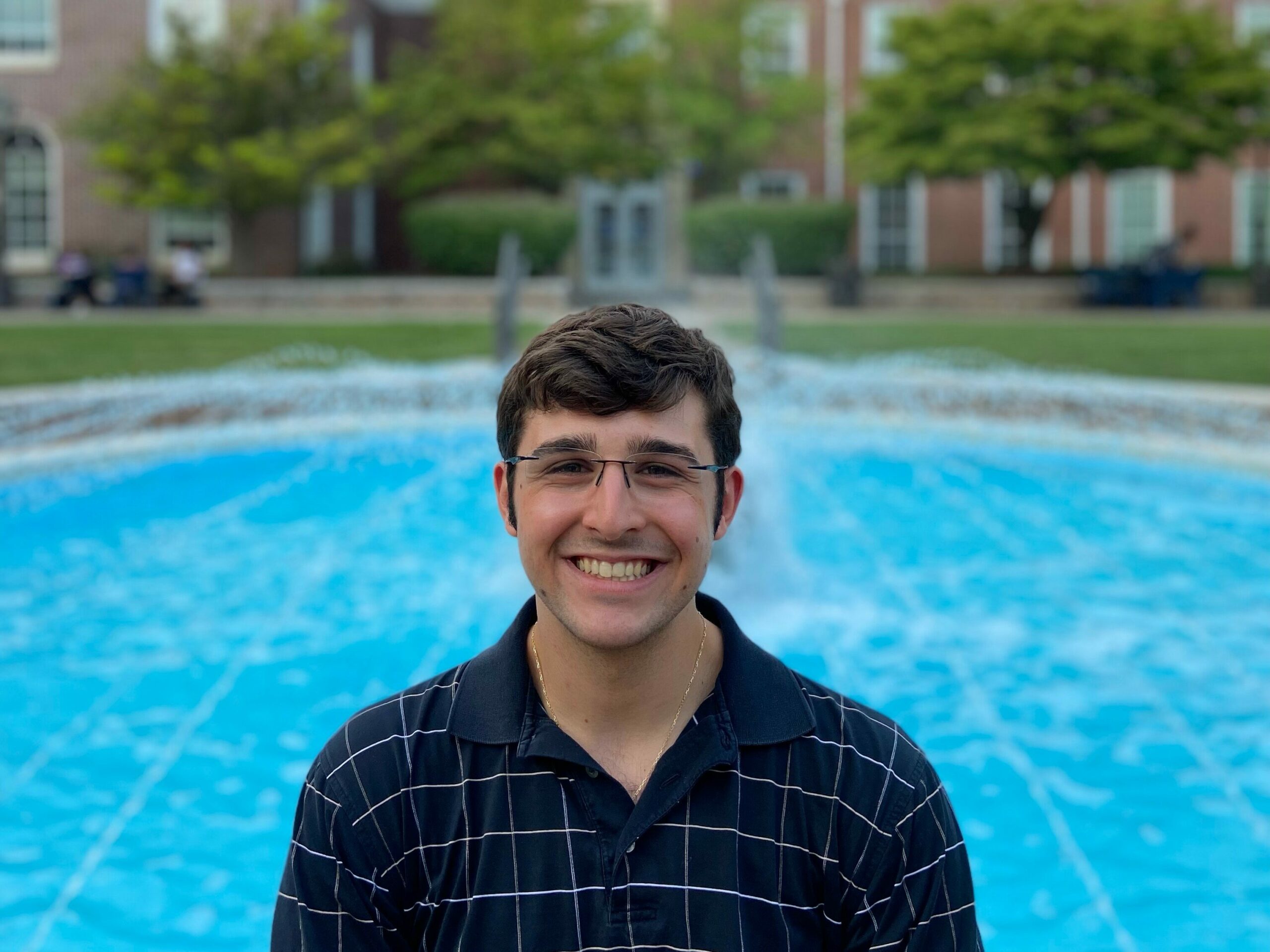
Spencer is the team leader. He managed the project, communicated to faculty and staff members, organized and ran meetings, and held group members accountable for their roles. Spencer also designed and programmed the electronic system on the device. He led the implementation of the electronic system onto the device and led the verification of specifications and validation of requirements relating to the electronic system. In addition, Spencer machined tubing for the device, rolled the curve and the reinforcement curve, and aided device assembly. He also performed verification and validation tests relating to other non-electronic aspects of the device. Additionally, Spencer and John modeled the bottom of the device as a spring to estimate energy expenditure and spring constant metrics. Spencer also collaborated with Eugene on the 3D printing and with David on the computer modeling.
Eugene Kim – Finite Element Analysis / Webmaster
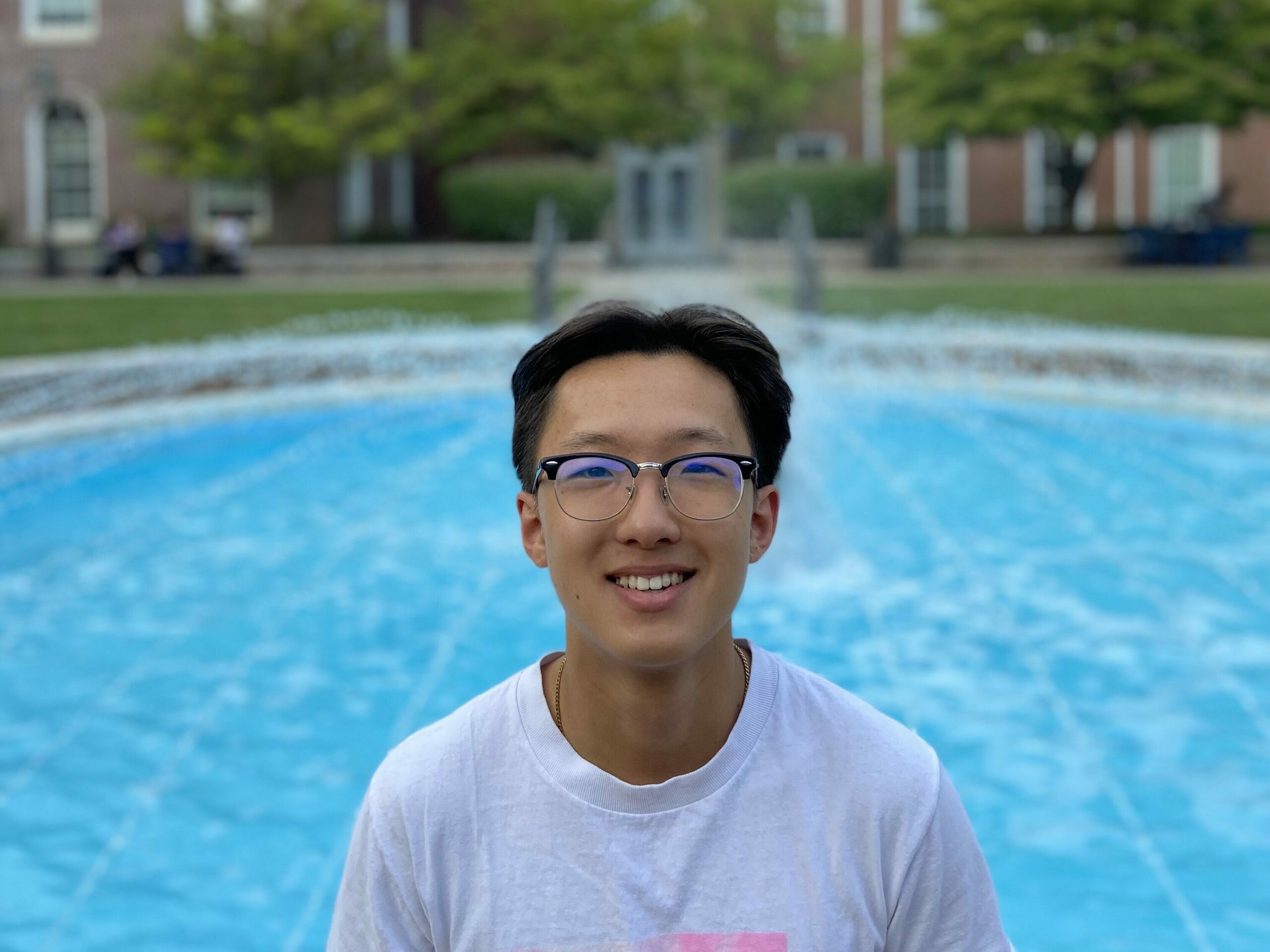
Eugene Kim was responsible for finite element analysis and contributed to CAD modeling of the device. He configured and ran force tests in Ansys to ensure the structural integrity of the device and created and revised CAD models of designs for the reinforced curve, the handle, and the body of the device. Eugene led the process of machining all device parts and assembling the complete device, along with David. He was in charge of coordinating machine shop jobs such as welding and waterjet cutting, as well as 3D printing of the axillary support and load cell inserts. He performed both verification and validation testing for the mechanical aspects of the device, and aided with the implementation of the electronic system onto the mechanical frame. Additionally, Eugene maintained the project website.