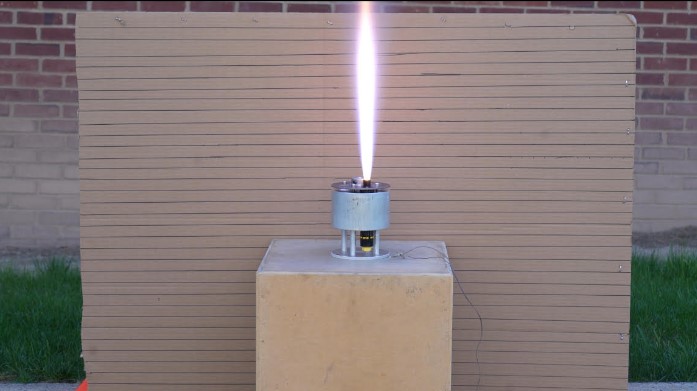
The team ignited one of the thrusters inside the mounting mechanism in order to see how large of a flame is let off. The flame was 16 inches long.
The team ignited one of the thrusters inside the mounting mechanism in order to see how large of a flame is let off. The flame was 16 inches long.
With the vacuum chamber and mounting mechanism manufacturing being complete, the team will begin testing their TARPP design soon. This will provide the team the appropriate data they need to show that the TARPP design is a viable solution to help mitigate the lunar dust interaction with the payload.
On April 8th, 2024, the team began to manufacture the mounting mechanism. The manufacturing of the mount was then finished on April 9th, 2024.
On April 2nd, 2024, the team put the chamber under vacuum for the first time. The chamber got to a pressure of -21.5 inch of mercury vacuum level before the glue on the edges cracked. Because of this crack, the team needed to reseal the edges and wait a few days before testing again.
Drawings for the mounting mechanism were completed. Manufacturing of the mount scheduled to begin soon.
The team was notified that they have been selected as finalists for the competition. The team will be traveling to Huntsville, Alabama at the end of June and will be competing against 11 other schools from across the country.
On March 22nd, 2024, the team finished cutting and manufacturing the acrylic for the vacuum chamber. The team then started to assemble and epoxy the panels together. This allowed for the epoxy to cure over the weekend.
March 13th, 2024 marks the first day of major manufacturing for the team. On this day, the acrylic started to be cut for the vacuum chamber design. The team would continue to meet throughout this week and cut out the rest of the acrylic.
After some redesigning, the team started to receive the material ordered in February. This allowed for a smooth transition from designing to manufacturing.
While looking to update and finalize drawings, the team has begun ordering parts to start manufacturing. The team has also begun looking into simulations and the use of the Jet Engine in the lab in order to begin using the lidar sensors and cameras. This will allow for the team to transition smoothly into the use of the sensors and cameras in the vacuum chamber.