Base
To make the mold for manufacturing the base, the base was first 3D printed so the mold could be formed around it. A wooden frame wrapped in saran wrap was first constructed in order to create a smooth, non-stick area for the mold to form. Clay was then placed at the bottom of the frame to leave room for the second half of the mold. Ecoflex Silicone Rubber was then added to the top of the base model and was set to form over 4 hours. The mold was produced in two separate halves. Once the mold was created, the mold was sprayed with mold release, sealed with rubber bands, and a funnel was inserted into the mold to allow for the casting material to flow in.
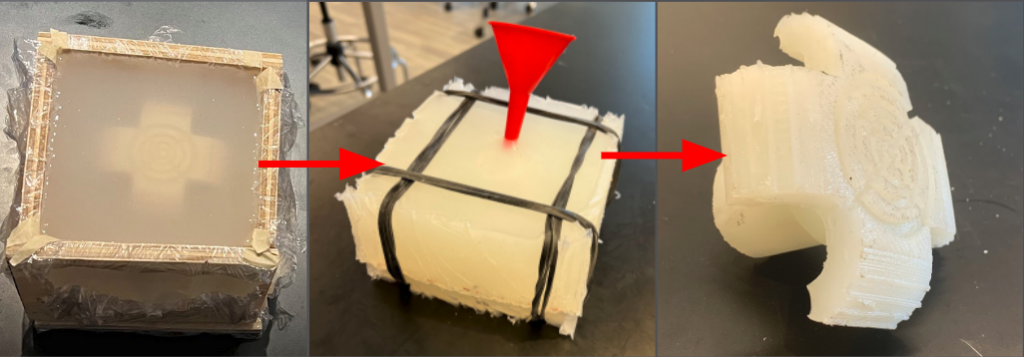
Axillary Padding
First, a two-part mold was created in SolidWorks consisting of a rectangular space with indents for lining up the two sections. This mold contained the outline of the padding shape within it as well as three additional 0.5’’ holes leading to the top. The center one was the main entry for pouring the silicone rubber cast material into the mold. Due to the upward curve of the shape, the left and right holes needed to be added because once the lowest part filled up to the hole, the silicone would not travel to the curved parts to fill the shape. Adding the additional holes allows for two more entry points that allow the cast material to travel and fill up the sides of the mold space. The silicone cast material was made from a 2 part mix, combining 100g of “Part A” to 1g of “Part B” and mixing for 5 minutes. Once the silicone cast was done being mixed, the silicone was poured into the mold and left to set for a period of 1 day. The mold was then broken apart to take out the final molded piece.
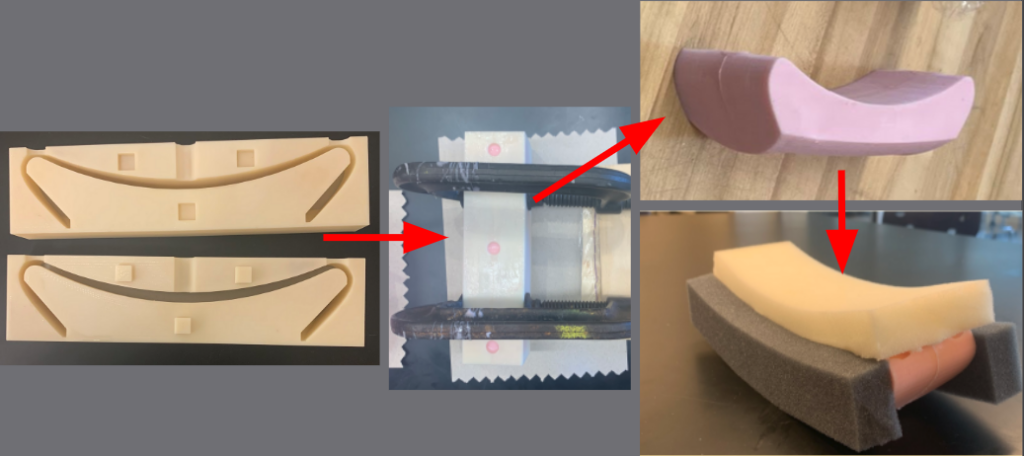
Sitting to Standing Component
The sitting to standing component was made out of a block of Nylon 6/6. The manufacturing operator used a water jet to carve out handles from the block according to the drawing specifications. This handle was then rounded at the edges using a dremel in order to fit the user’s hand more comfortably.
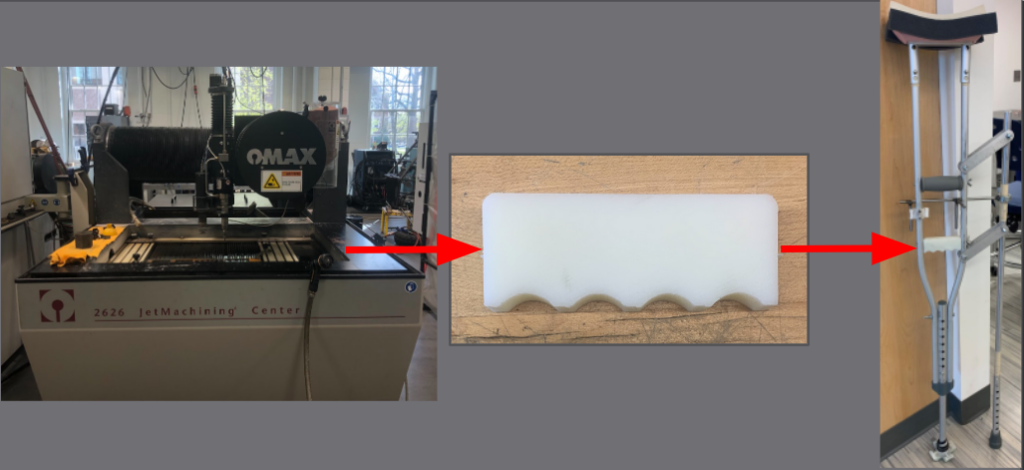
Stair Stability Component
The milling machines and hand drills from the TCNJ manufacturing lab were primarily used to create the stair components of the device.
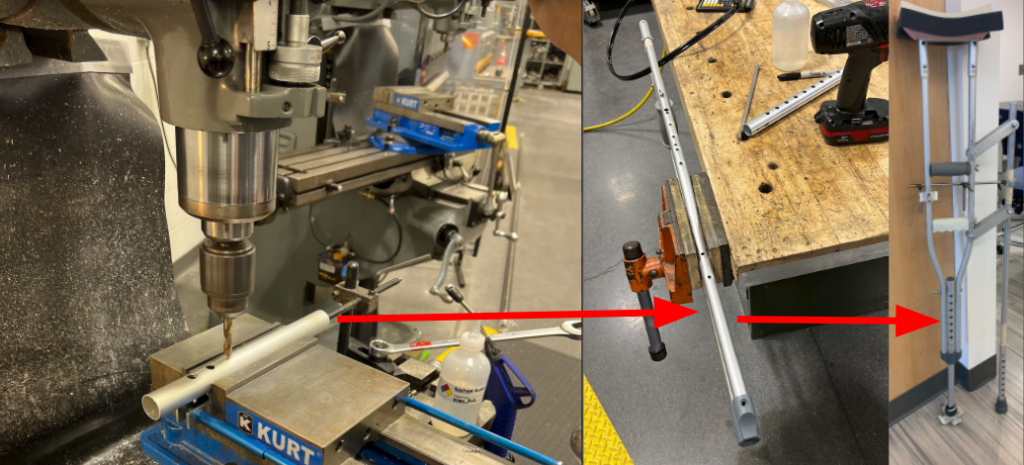