Week 13 (April 26th-May3rd)
The testing process was difficult once all the parts were made and the sawbones were prepared. To represent the device being implanted, sawbones were used as a substitute for femoral bones. The sawbones were cut such that the bottom would fit into the Instron grips. A lathe was used to drill holes into the sawbones and the device was hammered in. Our team planned to cut the first sawbones by drilling holes in the bone. We first tried drilling cylindrical holes into the sawbones using 3 different drill bit sizes, but we quickly realized that this was not going to work since those bones broke during the hammering process. We then tried drilling in a ⅞ and 1in holes side by side to make room for the slanted edge of the device (point to it). This also ended up breaking but seemed more promising. The final sawbones trial used the same 2 holes with an extra 11/16 inch drill bit down the middle to possibly create more room but this ended up making the device too loose. It didn’t seem like the pins were necessarily able to come into contact with the bone as desired since cylindrical holes were used.
Since we were not able to use the sawbones to its potential our team decided to perform a compression test on the actual prototype to gather data, however, it cannot be verified due to the implant being tested without a sawbone; no matter if it passed or not. It was also not possible to perform mechanical testing to verify specification 5 and 6 due to the time constraint and lack of materials. However, through ANSYS simulation, it was found that the device passed the verification activity for specification 1, 2, 5, and 6; therefore, the device is also validated due to the way that the requirements were written. Here is an image of the steel implant with the pins ejected out:
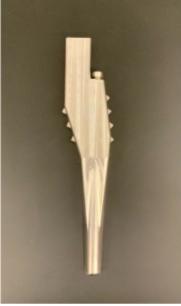
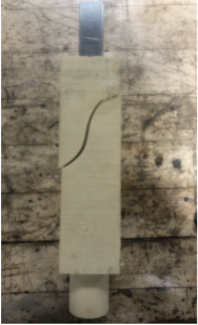
Here is a summary of the verification and validation activities that were done:
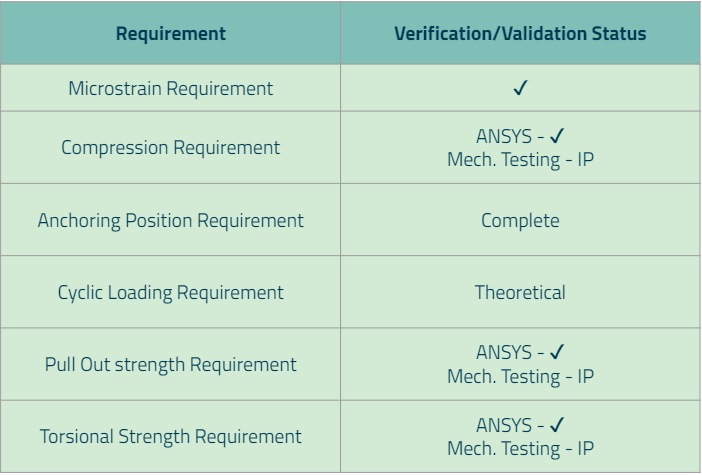
In the future, our team would like to refine the full scale ANSYS simulation to better understand the strain behavior. Throughout this project, we simplified our model to obtain data, however, it did not give us the full story of how the implant would have handled our requirements when considering all parts (pins, screws, etc.) We would also like to do ANSYS dynamic load testing to obtain realistic data. Lastly, to obtain equipment to properly prepare sawbones and to test porotype with titanium rather than stainless steel
And this concludes our senior project. Thank you for taking the time to learn more about our project throughout the year!
Thank you Dr. Wagner for your support and guidance throughout this yearlong project.