As components of the gimbal rig were being manufactured in the Machine Shop, students were simultaneously assembling the rings to get a visualization of the final product. Students worked diligently in order to have a gimbal rig ready for continuous testing of the manual and autonomous features in the drone.
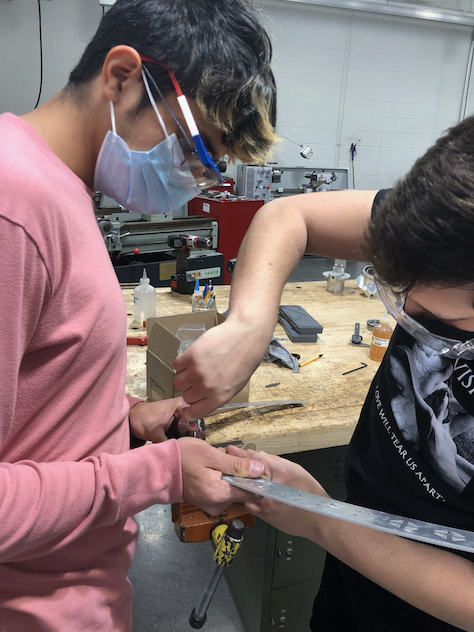
Here, we have William and Fabian attached the aluminum rings to the 3D printed sleeve bearing. Previously, the holes on the sleeve bearings were also tapped in order to have the screw go through.
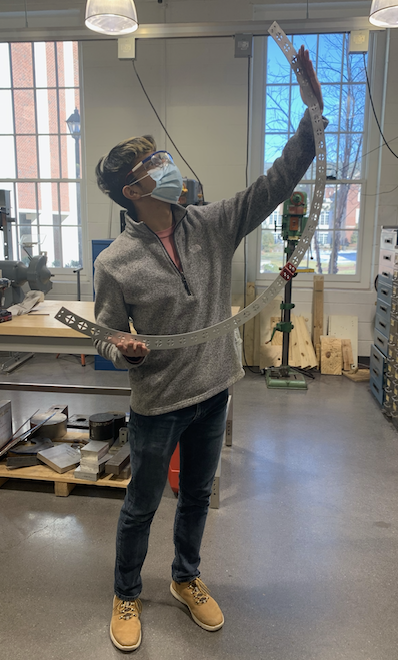
Here, we have Fabian posing with a half assembled ring after connecting the sleeve bearings to the two yaw rings.