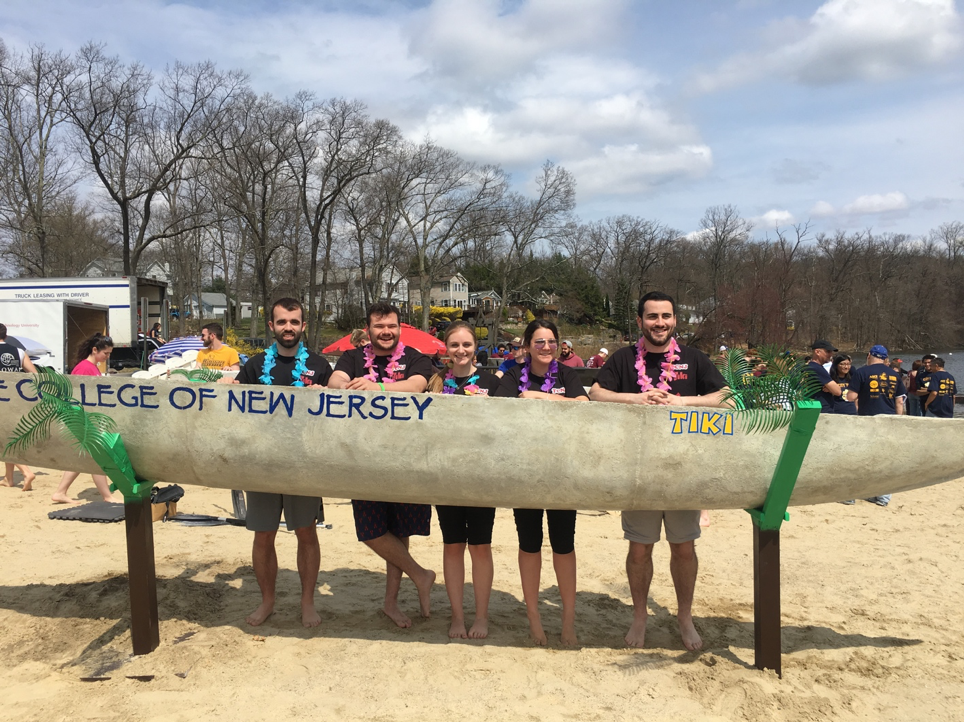
On Sunday, April 14, ASCE held its Metropolitan Conference for the Concrete Canoe Competition at Cooks Pond in Denville. Showing up wearing their hula skirts and leis, TCNJ Tiki went into the day with a positive attitude and was looking forward to seeing their hard work put to the test succeed.
The morning began with inspection of both the canoe and the display table. The display table included a poster outline the design components, a copy of the design report, 500 mL samples of all cementitious materials and aggregates used, a 1’ x 1’ sample of reinforcing mesh, and 2 cylinders of the mix design selected. Additionally, a 4’ display section of the canoe demonstrating the application of the concrete and mesh was included.
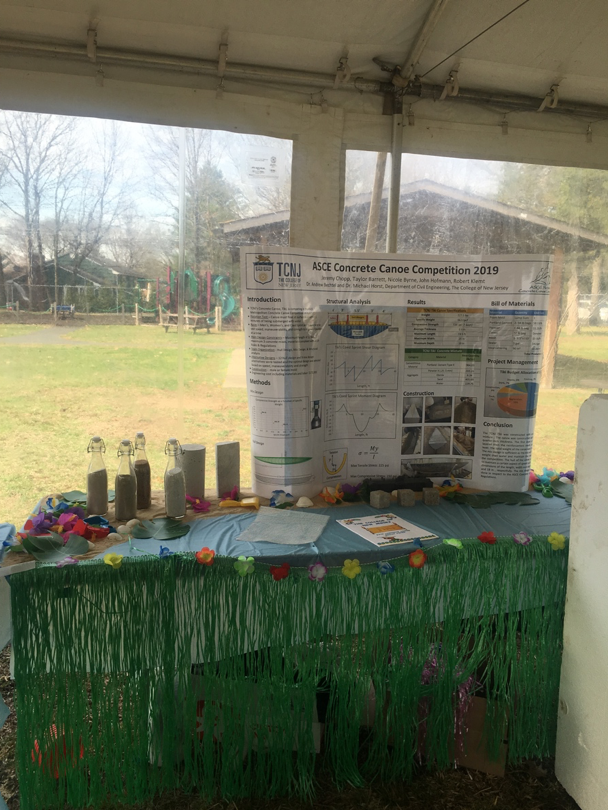
As the day moved on, the first event was the Swamp Test. The team must submerge the canoe under water, and it must float back up to the surface within 2 minutes, and the canoe was successful!
The next event of the day was the Sprint Race. In both a male and female race, two team members must paddle from the starting line, to a buoy on the other side of the lake and back in the fastest time possible. The male team consisted of Bobby and Jack, who struggled to maneuver the canoe and were forced to jump out and swim to shore. The team realized the boys had taken the canoe out backwards, which made it hard to maneuver. The female team consisted of Taylor and Nicole. After correcting the problem of the backwards canoe, the girls took second overall with a time of 3 minutes and 18 seconds. Lastly, the co-ed race consisted of two laps back and forth across the lake, and had a team of four team members in the canoe, Jeremy, Jack, Nicole, and Taylor. The team worked together and got fourth place, with a time of 6 minutes and 18 seconds.
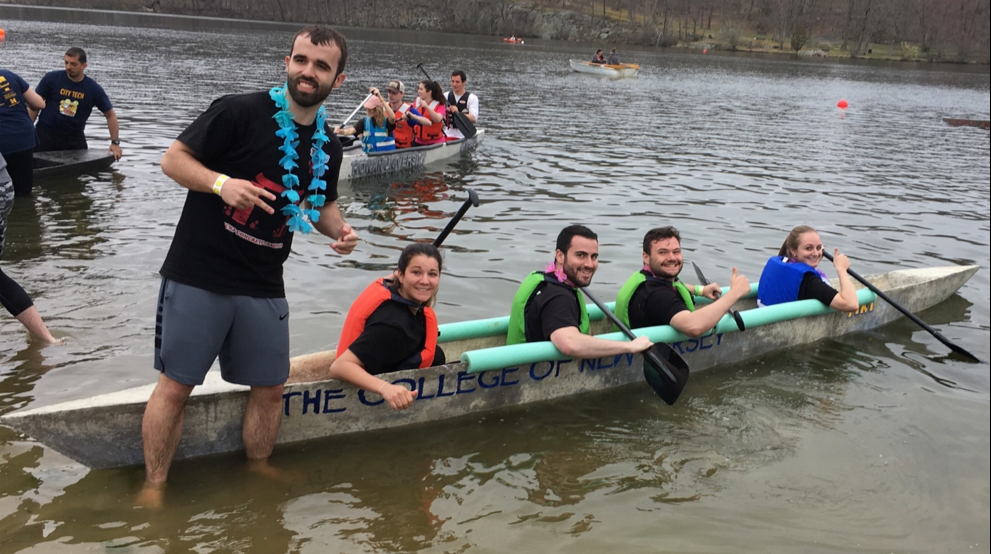
Overall, it was an exciting and successful day, and the team placed 5th place overall in the competition.