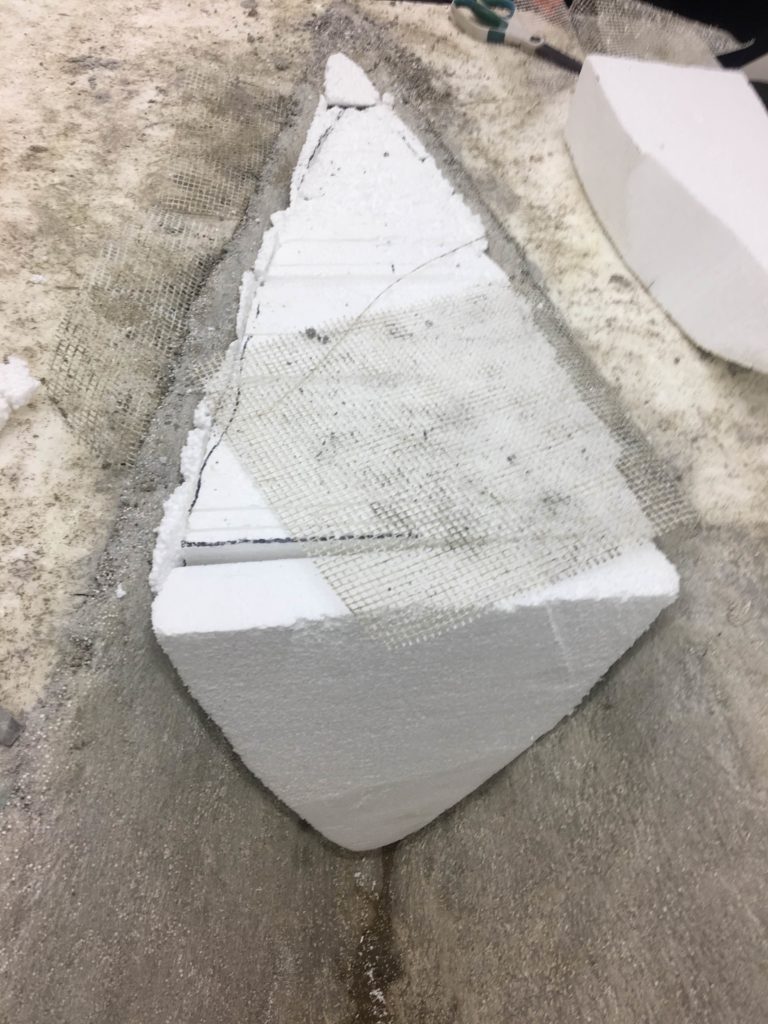
The team came back from spring break ready to cut and place the styrofoam blocks to fit in each end. According to the rules and regulations, the flotation must be within 3 feet of both the bow and stern. The foam block was created by cutting several cross sections in plan view and securing them together. The pieces were first cut using the workshop’s band saw and shaved down using a rasp to fit into the shape of the canoe. Finally, a cross section piece was placed on the inside to act as a smooth wall going from the bottom to the top of the canoe. To place the foam down, a thin layer of our mix was placed on the canoe where the foam blocks would be installed. The foam was then covered by concrete and the